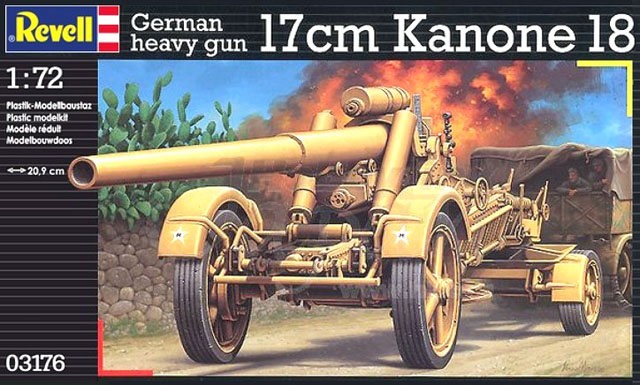
I started removing some parts
from the sprues a few weeks after receiving it, then I halted the
project to finish other ongoing projects. After realizing the I had
Trumpeter Famo in my stash, along with my Sd.Kfz.253 project halted a
long time ago, plus several options for village and farm houses, I
started to plan a new diorama. I won't reveal it now, let me stick with
Revell's Kanone 18 here. It is a wonderful kit, very detailed and
engineered for the most part. Although I've been building some armor
models in 1/72 from times to times, this one really impressed me for
the quality of the moldings, rivets, and detailed subassemblies. The
kit can be posed in firing or transport configurations, and rivals many
old kits in 1/35 scale.
Anyway, back to the kit, I started
gluing the cannon barrel. I know there's this insane trend for metal
barrels, but honestly folks, if there is nothing wrong with the kit
parts, and you are probably going to paint the model anyway, why to
replace them? I know there are nasty examples out there, but this was
not the case. I used pieces of brass tubing to keep a perfect alignment
of the barrel halves while the glue dried, and it worked like a charm:
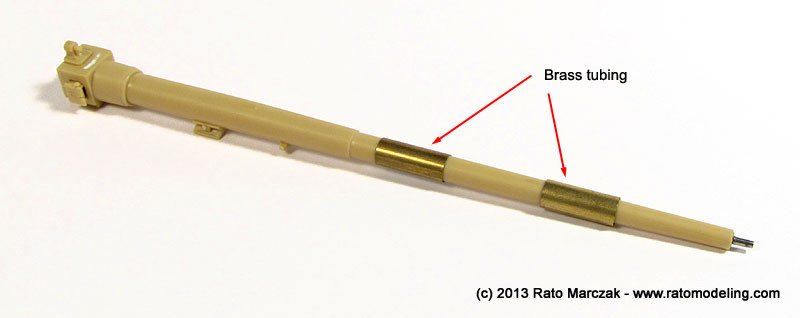
Once dry, I devised a method to try to simulate the barrel grooves. First, I had to sort
through my spare parts box for a clock gear with a diameter slightly
larger than the internal diameter of the barrel. Using lots of liquid
glue, the gear was press fitted inside the barrel. The pressure and the
liquid glue allowed the gear teeth to make visible impressions in the
barrel. Once the glue was dry, the gear was removed leaving a
reasonable rendition of the grooves (I know they should be helical, but
then you are asking for too much):
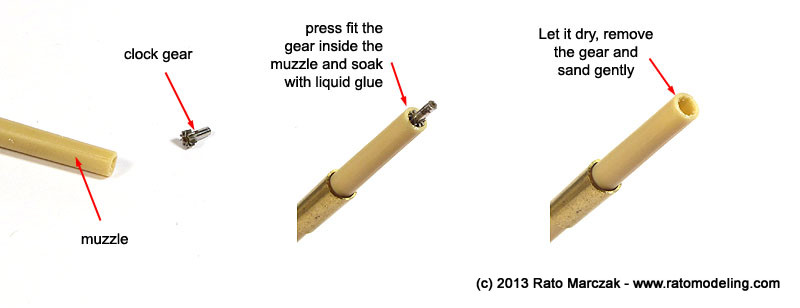